I’m doing a little bit of consultancy for the windfarm at the moment, so didn’t get started on the boat till lunchtime. But I managed to extract the watermaker from the bilge area where it lives, As predicted it was difficult, it was bolted to a piece of wood, with the nuts underneath. This wood was then fixed to the bilge with more bolts, or screws, or glue. I couldn’t tell, because the deck-wash and water pumps were fitted over the fixings, these pumps were plumbed in rather rigidly making the whole affair rather complicated. Fortunately I found a ring spanner I could get underneath the wood to fit on the nut, unfortunately I only caught 3 out of 4 nuts as they came off, but I was happy enough to have kept the spanner from going under the fuel tanks in the bilge.
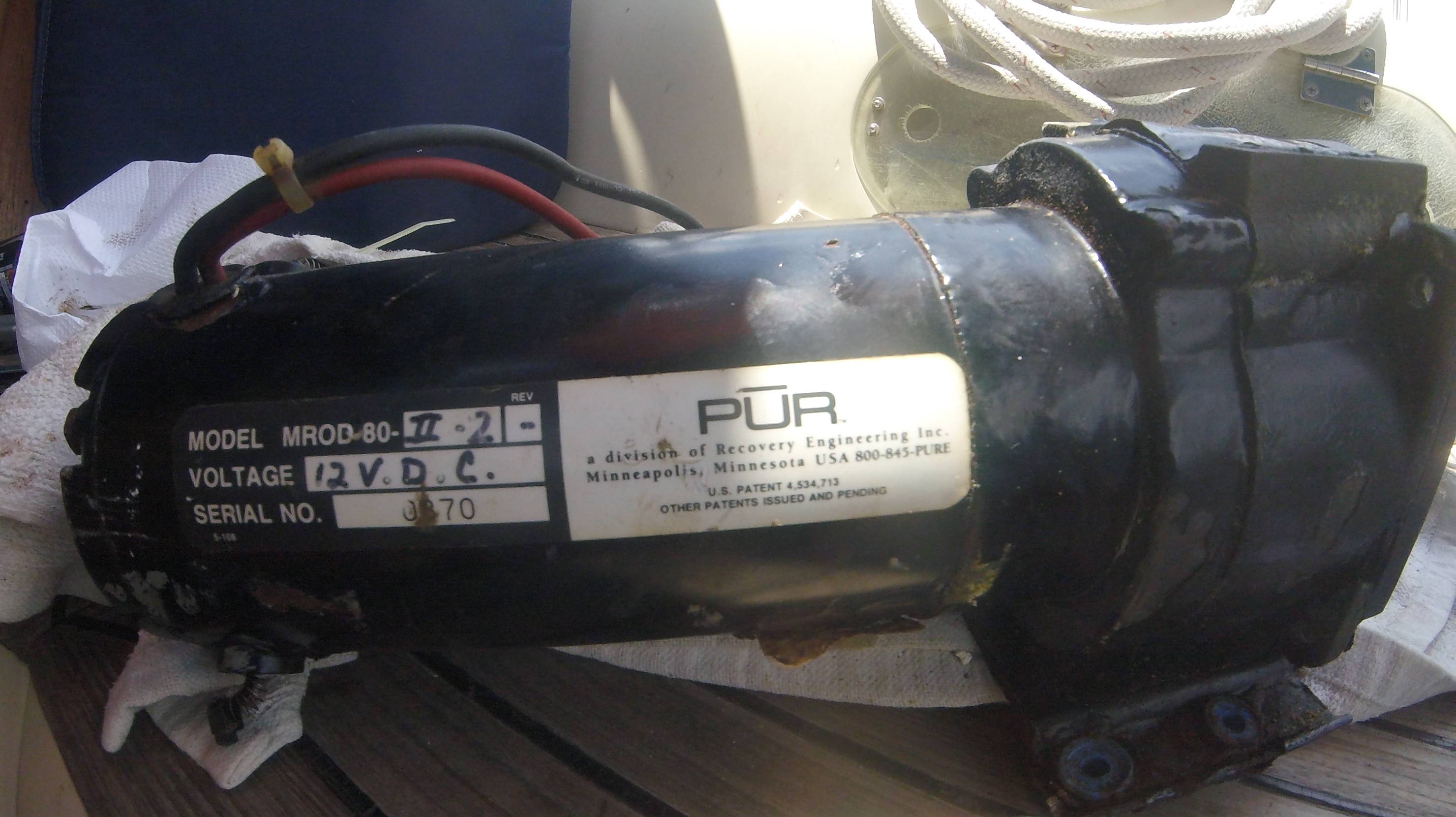
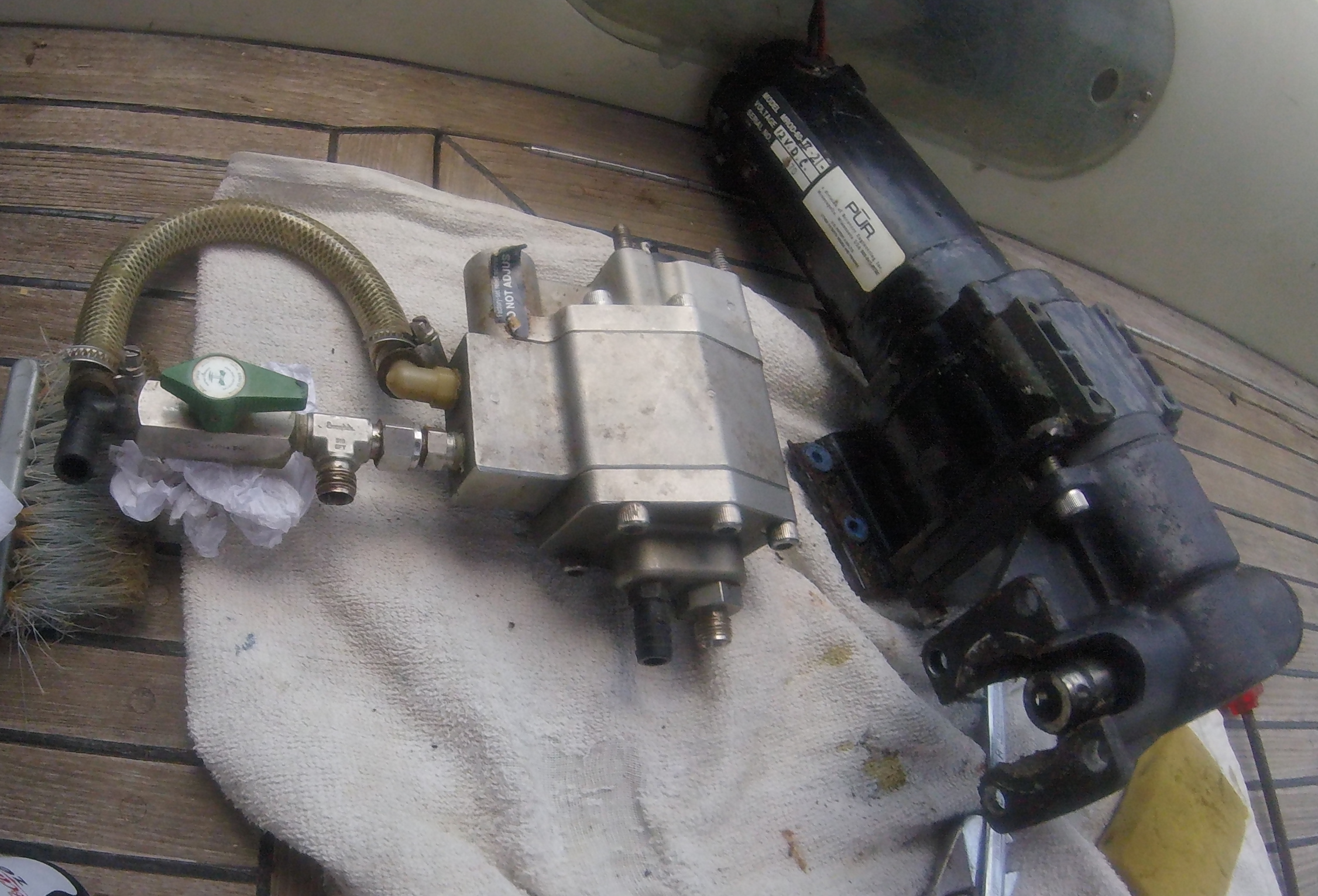
So I took the Drive unit, or motor as I would call it apart. I love taking things apart, and this was quite easy, especially with the manufacturers instructions handy.It became apparent quite quickly where the problem was, water must have been getting to the outside of the motor end cap, and had found a way into the motor.
You can see a lot of white powder, this looks like aluminium oxide to me, or an oxide of whatever the motor casing is made of. The cap / end cover from the motor has a bit missing, this is what became the white powder, or oxide (rust). the presence of water has caused some other rust, not a lot, but the brushes that carry the power to the coils were/are seized in their carriers and don’t make contact with the armature, or is it a commutator?
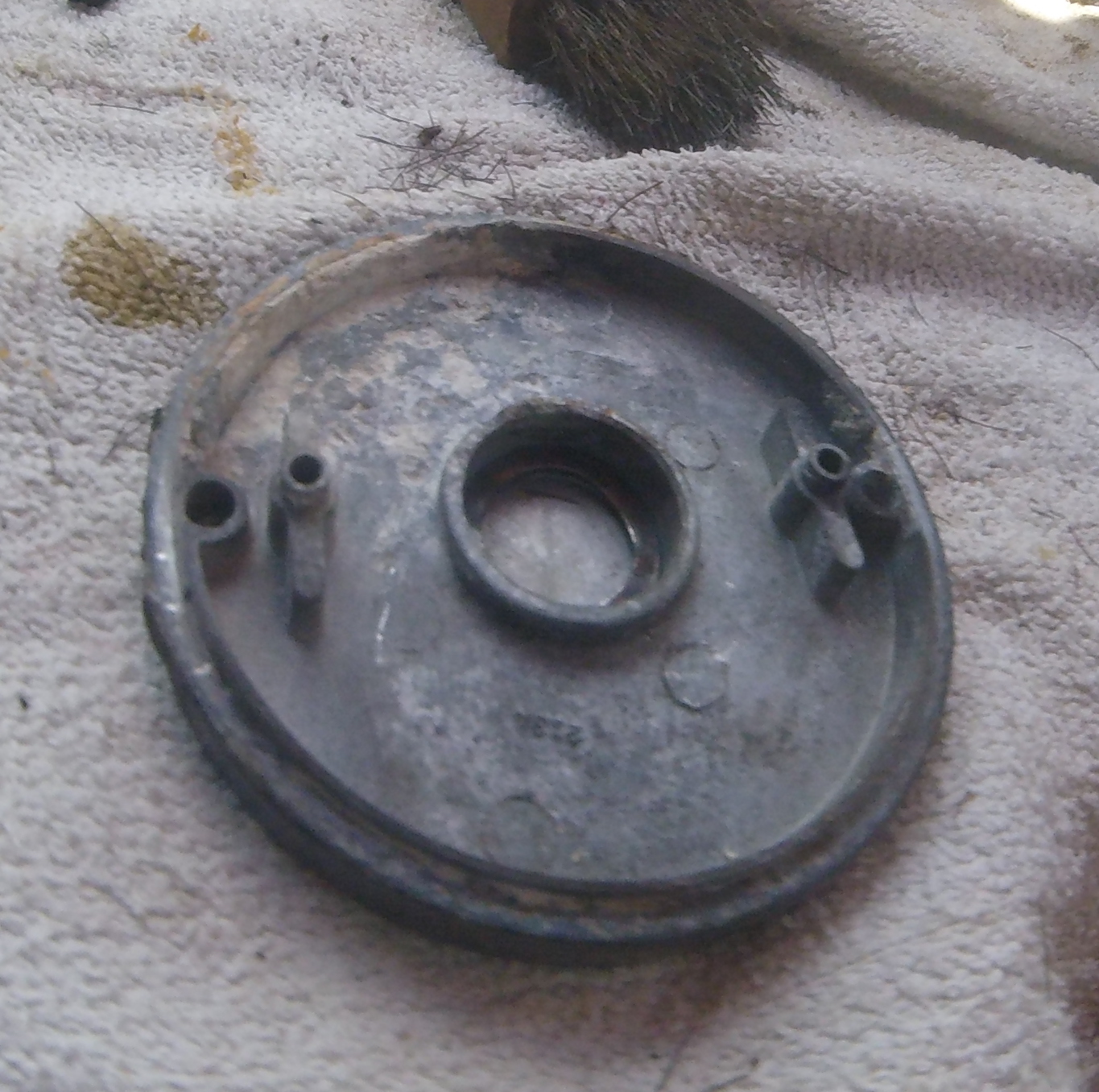
I could fix this up, I need to get new carbon brushes, probably not that hard here if you know where to go. I could use some epoxy resin to fix the end cap. I moved my attention to the gearbox at the end of the motor, where the direction of rotation is turned into a piston like action and found a crack in the casing. I don’t think it matters actually, but I couldn’t get the piston to budge, so either it’s seized in the gearbox, or the gearing is so high I wouldn’t be able to anyway.
By now I’m wondering what’s actually ok, the membrane housing should be ok, presumably the high pressure hoses will be ok, Im replacing all the fresh water hoses anyway, but they’re pennies. The high pressure pump looks ok, but until I can run it I won’t know if its ok. Presumably it’s feeling its age too.
I’m thinking I might not be putting this back together again. I packed all the bits up, wrapped them up, and they are in a locker now. I sent off a few emails, to the manufacturer and to a spares stockist to get prices for a new motor/gearbox. I will wait and see what happens. A similar brand new watermaker is about $6500 USD. I think it can wait until we reach the states, our longest passage will be about 5 weeks and we can do that on our tanks without any problem, might need to get one of those deck solar shower jobs and fill with rainwater. I think the watermaker will come into it’s own when we cross the pacific on the way back, where we will go for months at anchor, and this saves us lugging jerry cans of water back and forth in the dinghy.
I’m coming to the opinion that very few things on a boat get to enjoy an 11th birthday, ten years seems about the most you can expect from electrical or fancy mechanical kit. My Macbook air is playing up now, which is devastating, but I can see corrosion inside the USB and charging connectors. I do need an excuse to buy the latest and greatest macbook, but not if it’s going to fail within a year too.
I spoke to the local boatyard today and arranged to visit in the morning to see what it’s like and get some commitment on the cost of the cutless bearing job and when it can be done.
Kathy hits the sky tomorrow, looking forward to her arrival, you won’t believe how high the dirty dishes are stacked 😉
Paul Collister
DCIM120GOPRO
Yep, that is a commutator that the brushes ride on, would think its repairable, locals know how to wash it, and put it in a oven for a few days. I wouldn’t trust them with sourcing brushes, unless you can get a equivalent, brush hardness is key. Too hard they wear the commutator. space between commutator segments must be clean. Resistance everywhere must be greater than 1 meg ohm, preferably infinity. Use locals to pull the HP pump and gearbox apart. I say that cose you can waste so much time.